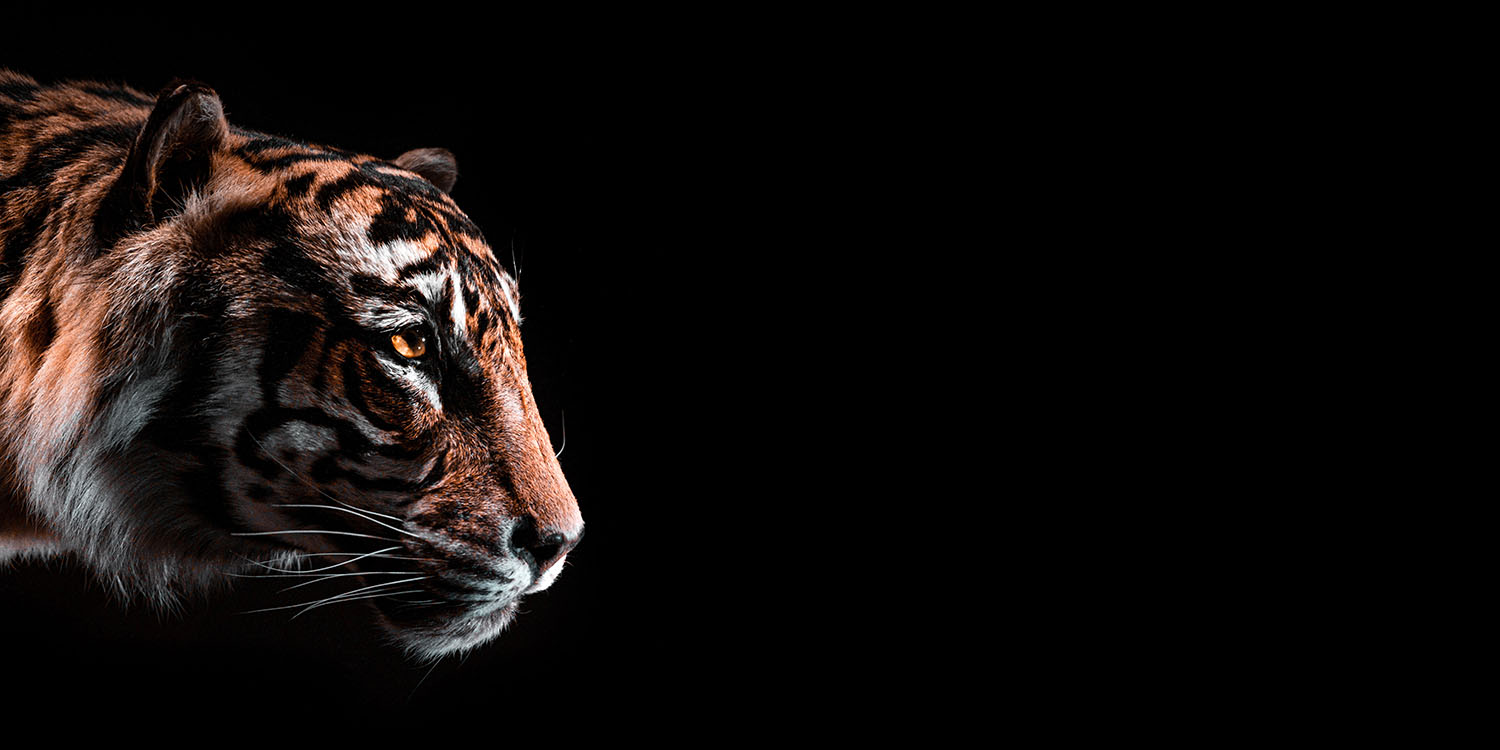
A new report says that Apple tiger teams involving hundreds of employees are working on reexamining the company’s supply chain – all the way down to screws and plastic inserts.
The goal is to ensure backup suppliers for every component, as well as to reduce dependence on China …
Apple tiger teams
The term “tiger teams” was first coined way back in 1964 to describe cross-disciplinary teams brought together to take an aggressive and rapid approach to problem-solving – where no potential solution is off the table, and no respect need be shown to past ways of doing things.
The most famous example was the Apollo 13 troubleshooting team, originally named the White Team, and later renamed the Tiger Team. They were awarded the Presidential Medal of Freedom for saving the astronauts aboard the module.
It’s common for these teams to report directly to very senior execs, and in Apple’s case, Bloomberg reports that CEO Tim Cook has direct involvement.
Reducing dependence on China
We’ve been warning for many years about both the need and the difficulty of reducing Apple’s dependence on China, but the pandemic made even clearer the risks of the company having most of its manufacturing eggs in one basket. COVID-19-related disruption at the world’s biggest iPhone assembly plant was estimated to have cost the company a billion dollars per week.
During Cook’s recent visit to China, he praised the “symbiotic relationship” the company enjoys with the country – while his tiger teams were hard at work to reduce the extent of it.
Even as Cook was smoothing things over in Beijing, Apple executives were hard at work developing ties to other countries to lessen reliance on the country, according to multiple people familiar with Apple’s operations […]
Apple’s efforts center on India as a location for production of iPhones and accessories, Vietnam for AirPods and Mac assembly, Malaysia for some Mac production, and Ireland—where suppliers currently build the relatively easy-to-produce iMacs—for a range of simpler products. Managers in Apple’s operations department have instructed employees to focus on sourcing additional components and locating production lines outside China for more new products coming in 2024.
Backup suppliers
Apple has always liked to have multiple suppliers for as many components as possible. This lessens the risks of relying on a single company, and also enables the iPhone maker to play multiple suppliers against each other in order to negotiate the best possible terms.
But the pandemic made backup suppliers even more important, and today’s report says that the company is now taking this to new levels of detail, within China as well as outside it.
It has expanded the efforts of these teams, which set up shop in suppliers’ factories in China and other countries, assess facility maintenance schedules, and assemble more extensive lists of backup suppliers for every component, right down to screws and plastic inserts. The company is working to improve its forecasts, component by component, to better anticipate potential shortages.
Fear of Chinese retaliation
While the tiger teams are geared to rapid change, there are hurdles to be overcome – including retaliation by the Chinese government, or push-back from Chinese consumers.
Apple’s leadership is concerned that China might retaliate if it moves too much capacity to other countries, or transitions too rapidly. Customers in China could turn against US-designed products amid heightened nationalism. The company also has concerns about its ability to ensure high standards of quality in Vietnam and particularly Malaysia, given the current state of the manufacturing industries in those countries.
The piece also notes that there may be conflicts between the product development teams – which want to take full advantage of new tech, even if there is only one supplier, based in China – while the procurement team will be arguing against such dependence.
The full piece is worth reading.
Photo: Efe Yağız Soysal/Unsplash
FTC: We use income earning auto affiliate links. More.

Comments